bending and cutting sheet metal The bending of sheet metal allows a wide variety of part geometries to be produced and is particularly useful when performed alongside cutting. The most commonly used method for each process is CNC laser cutting and brake press bending. In recent times, advancements in engineering have pushed the boundaries of CNC technology, resulting in the creation of the largest CNC machine ever built. In this blog post, we will explore the journey of this colossal machine, its capabilities, and its impact on the manufacturing industry. The Genesis of an Engineering Marvel.Whether you’re looking for a CNC router, mill, lathe, or laser machine, it’s important to shop with reliable brands that provide top quality machines and great customer support. However, with so many different .
0 · universal sheet metal machine
1 · types of sheet metal benders
2 · sheet metal bending near me
3 · sheet metal bending diagram
4 · sheet metal bending design guide
5 · sheet metal bending basics
6 · problems with sheet metal bending
7 · maximum thickness sheet metal bending
Fig 2: Working Principle of CNC machine. The process of CNC machining involves several integral components working seamlessly in tandem. Initially, the part program is input into the MCU (Machine Control Unit) of the CNC system.
universal sheet metal machine
china custom metal welding parts
The bending of sheet metal allows a wide variety of part geometries to be produced and is particularly useful when performed alongside cutting. The most commonly used method for each process is CNC laser cutting and brake press bending. Improve your sheet metal bending techniques with these 8 design guidelines. Learn how to create precise bends and avoid costly mistakes. Sheet metal fabrication is a complex manufacturing process that includes cutting, bending, hole punching, embossing, and many other forming operations. As the parts have .The bending of sheet metal allows a wide variety of part geometries to be produced and is particularly useful when performed alongside cutting. The most commonly used method for each process is CNC laser cutting and brake press bending.
From basic concepts to advanced techniques, this guide covers everything you need to know about sheet metal bending. Learn about the different bending methods, tools, and tips to achieve accurate and high-quality results.
Improve your sheet metal bending techniques with these 8 design guidelines. Learn how to create precise bends and avoid costly mistakes. Sheet metal fabrication is a complex manufacturing process that includes cutting, bending, hole punching, embossing, and many other forming operations. As the parts have more features, the complexity of the design also increases. Therefore, you must consider the sheet metal design guidelines to ensure manufacturability. Sheet metal bending can be done using many methods. We discuss those along with springback, bend allowances, k factor, design tips etc.In this comprehensive guide, we delve into the intricate processes of Sheet Metal Bending, the vital role of Press Brakes, and the transformative impact they have in industries ranging from automotive to aerospace.
Sheet metal bending is the forming of metal into different geometries, by using a force to deform the metal. It is referred to as sheet metal bending as a thin sheet of metal is bent once, or multiple times, to form the final geometry. The thickness of sheet metal used can vary.
Bending sheet metal is a meticulous process. It involves a series of steps, starting from picking the correct type of metal, marking the bend lines, securing the metal on a bending brake, and finally applying the right amount of pressure to make the bend.Bending is a fundamental process in sheet metal working that involves deforming a metal workpiece into a desired shape by applying force between two tools by a press brake: an upper tool (known as a punch) and a bottom tool (known as a V-die). Have you ever wondered how to achieve perfect sheet metal bends? This article dives into essential bending techniques, exploring everything from calculating material expansion to selecting the right tools. You’ll learn how to tackle common challenges, ensuring high-quality, efficient production.
types of sheet metal benders
The bending of sheet metal allows a wide variety of part geometries to be produced and is particularly useful when performed alongside cutting. The most commonly used method for each process is CNC laser cutting and brake press bending. From basic concepts to advanced techniques, this guide covers everything you need to know about sheet metal bending. Learn about the different bending methods, tools, and tips to achieve accurate and high-quality results. Improve your sheet metal bending techniques with these 8 design guidelines. Learn how to create precise bends and avoid costly mistakes. Sheet metal fabrication is a complex manufacturing process that includes cutting, bending, hole punching, embossing, and many other forming operations. As the parts have more features, the complexity of the design also increases. Therefore, you must consider the sheet metal design guidelines to ensure manufacturability.
Sheet metal bending can be done using many methods. We discuss those along with springback, bend allowances, k factor, design tips etc.
In this comprehensive guide, we delve into the intricate processes of Sheet Metal Bending, the vital role of Press Brakes, and the transformative impact they have in industries ranging from automotive to aerospace. Sheet metal bending is the forming of metal into different geometries, by using a force to deform the metal. It is referred to as sheet metal bending as a thin sheet of metal is bent once, or multiple times, to form the final geometry. The thickness of sheet metal used can vary.
Bending sheet metal is a meticulous process. It involves a series of steps, starting from picking the correct type of metal, marking the bend lines, securing the metal on a bending brake, and finally applying the right amount of pressure to make the bend.Bending is a fundamental process in sheet metal working that involves deforming a metal workpiece into a desired shape by applying force between two tools by a press brake: an upper tool (known as a punch) and a bottom tool (known as a V-die).

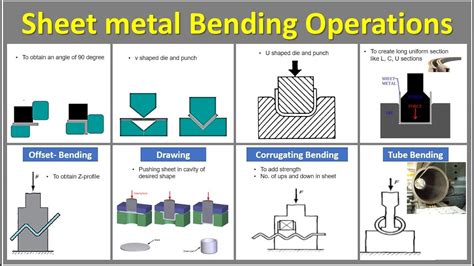
Reinforced steel and double base construction with a baked-enamel finish. Full-extension drawers with full-width designer pulls. Interlock system allows 1 drawer to open at a time. Heavy-duty, 3 .
bending and cutting sheet metal|problems with sheet metal bending