sheet metal minimum bend radius chart A typical recommendation is 1t for all sheet metal parts, which means the smallest bend radius should be at least equal to the sheet thickness. For example, if the thickness of the sheet is 2mm, the minimum bend radius . Since 2000, Watkins Metal Fabrication Inc. has been providing Fabricated Structural Metal from Mineral Wells. Watkins Metal Fabrication Inc. is incorporated in Texas.
0 · sheet metal bending chart
1 · sheet metal bend deduction chart
2 · minimum sheet metal hamtramck radius
3 · maximum thickness sheet metal bending
4 · bend radius chart sheet metal
5 · aluminum minimum bend radius chart
6 · 304 stainless steel bend radius
7 · 304 stainless minimum bend radius
$35.49
sheet metal bending chart
A typical recommendation is 1t for all sheet metal parts, which means the smallest bend radius should be at least equal to the sheet thickness. For example, if the thickness of the sheet is 2mm, the minimum bend radius .The bend radii listed are standard minimum if manufacturing for aircraft and aerospace applications. Since commercial sheet metal bending can be done with less concern for .The tables below show bend radii and minimum bend sizes for materials and tooling combinations stocked by Protocase. We go beyond the general rules of sheet metal bending, as our . Mild Steel: For materials with a thickness up to 1.2 mm, a minimum bend radius of 0.8T (T = material thickness) is recommended. Aluminum: A minimum bend radius of 2T is typically suggested for materials below 4 mm .
RECOMMENDED MINIMUM BEND RADII FOR 90-DEGREE COLD FORMING OF SHEET The radii listed are the minimum recommended for bending sheets and plates without fracturing in . Medium-carbon steels and some structural steels including 15, 20, Q235, Q235A, and 15F require a slightly larger minimum bend radius of 0.5t. Higher-carbon steels and higher-strength structural steels such as 25, 30, and .
stainless steel kitchen cabinets hyderabad
The tables below show bend radii and minimum bend sizes for materials and tooling combinations stocked by ProtoSpace Mfg. It is possible to choose other bends, but tooling charges may . The calculated 0.375-in. radius is the minimum producible inside radius for this material and not the recommended inside radius that you see on the bend allowance chart. It’s true that the harder and thicker the plate is, the .Sheet Metal Bend Radius Guidelines. Here are a few key concepts to know about designing for sheet metal. Brackets, covers, cabinets, chassis, electrical enclosures. These and countless other sheet metal components might seem . Learn the 20 percent rule to better predict the sheet metal inside bend radius when air forming during your welds, and find our sheet metal bend radius chart here. Our Sites . FMA; The Fabricator; FABTECH; . This chart .

Sheet Metal Bending Radius refers to the minimum radius that can be applied to a sheet metal component where its flange originates from. Bending radii are usually dictated by available tooling, and for quick and effective .Bending Radius Bending Radius refers to the minimum radius that can be applied to a sheet metal component where its flange originates from. Bending radii are usually dictated by available tooling, and for quick and effective design work it .
Grain direction is usually specified on stainless steel and other hard materials when it is necessary to maintain minimum bend radius or to control spring back on parts with large radius forms. . Aluminum Sheet Metal Size Table Chart . MATERIAL. SHEET THICKNESS--.012.016.020.025.032.040.050.063.071.080.090.100.125.160.190. 2024-0 & W.06.06.06 .The bend allowance and bend deduction are two measures that relate the bent length of a piece of sheet metal to the flat length. The bend allowance describes the length of the neutral axis between the bend lines, or in other words, the arc length of the bend. Therefore, the bend allowance added to the flange lengths is equal to the total flat . The minimum sheet metal bending height should be calculated as 2 times the thickness of the sheet metal plus the bending radius, i.e., H ≥ 2t + R. As illustrated in the accompanying figure, if the bending height is too low, the sheet metal is prone to deformation and twisting during the bending process , leading to suboptimal part shape and . IV. Press Brake Bend Radius Calculation. The 8 times rule is a general guideline for determining the V-shaped die opening, suggesting that the V-die opening should be 8 times the material thickness. However, there is no exact formula for determining the ideal bend radius for sheet metal, but under certain specified force conditions, the bend radius can be estimated .
The bend radius is a critical parameter in sheet metal fabrication, dictating the minimum radius one can bend a metal sheet without significant deformations. Calculating the correct bend radius is essential for ensuring the structural integrity and aesthetic of the finished product. Calculating Bend Radius in Air Forming
As a general recommendation, ±0.005 in. runs right at the limit of precision flat sheet metal in a job shop environment. For bent sheet metal, variation in the raw material thickness increases the recommended precision to ±0.010 in. per bend. Layout Method for Sheet Metal “Sheet metal stretches when it bends” is an oversimplification.
Factors Influencing the Minimum Bend Radius. The minimum bend radius of the sheet metal is affected by several factors, each of which is of specific importance in determining the most desirable degree of bend that would prevent collapse or paper deformation. tAng factors include:. Material Type: Different materials have varying levels of ductility and tensile strength, . When working with aluminum over sheet metal, several variables need to be considered. Aluminum is typically thicker and stronger, and requires more force to bend as well as consideration of edge conditions and punch nose radii.. This free chart outlines what bend radii is required for the approximate thickness of aluminum.We recommend printing it out to keep as a . Table of Contents. 1 Common Bend Radius Design Mistakes; 2 Sheet Metal Part Design for Manufacturing Tip. 2.0.1 UNABLE TO UNFOLD PART, SHEET METAL BEND RADIUS ISSUE RESOLVED; 3 How to implement the industry standard sheet metal bend radius. 3.1; 3.2 Your Partner in Precision Sheet Metal Design; 4 Sheet Metal Part Design for Manufacturing .
sheet metal bend deduction chart
You can derive the Bend Allowance (BA) by using the K , Bend Radius (R), Bend Angle (A) and Material Thickness using the formula below. BA=Pi*(R+K*T)*A/180. In this formula: K represents the K-factor. BA is the bend allowance. A is the bend angle. R .Bend Radius - As a rule, inside bend radius should be equal to material thickness. When the . Form height to thickness ratio – To determine the minimum form height for sheet metal use the following formula: D = 2.5T + R (see below) The height can be less but it required secondary
Bend Radii & Minimum Bend Sizes. The tables below will help you to choose values that are both manufacturable and meet your needs. If you need help choosing a value, contact us at [email protected] or 1-866-636-9905 and we can help.Aluminum Minimum Bend Radii for 90 Degree Cold Forming of Sheet and Plate. per The Aluminum Association, Inc. Alloy: Temper: RADII FOR VARIOUS THICKNESSES EXPRESSED IN TERMS OF THICKNESS “t”An Air Bend Force Chart, or Force Chart breaks down a number of key components of sheet metal bending in an easy to reference format. Being able to read a bend force chart is crucial for any Brake Press operator and sheet metal engineer. The gauge, inside radius, die opening, and minimum flange length are all interconnected through different equations and relationships, the .Bend Radius. Sheet metal bend brakes are used to bend material into the parts desired geometry. . as a guide when designing the minimum flange length possible with the tooling for different V blocks as well as the bend radius. The following charts are based on the Armada Air Force bend guide. . Sheet metal parts with a minimum of 0.9mm to .
In sheet metal bending, the K-factor is a crucial parameter that determines the amount of material elongation and deformation during the bending process. . The bend radius is the radius of the arc formed on the inside of the bend. It is a critical parameter that determines the minimum size of the bend. Its important to change this value in .Practical Application of the Sheet Metal Bend Radius Chart. In practice, the Sheet Metal Bend Radius Chart serves as a foundational tool for engineers, designers, and fabricators. By consulting the chart, professionals can: Determine the Minimum Bend Radius: Ensure that the bend radius does not fall below the minimum threshold for the selected .
The bend allowance chart is an essential resource for professionals working with sheet metal fabrication. It provides a comprehensive listing of key parameters such as material thickness, bending radius, bending angle, bend allowance, and bend deduction values for common materials.
The sheet metal bend radius refers to the minimum radius a sheet of metal can be bent without causing damage or deformation. In essence, it’s the inner radius of the bend that determines how tight a curve can be formed in the sheet metal. . Sheet Metal Bend Radius Chart. A sheet metal bend radius chart is a valuable tool that provides .Minimum Bend Radii: The minimum bend radius data shown in these charts is measured to the inside of the bend. The bend radii listed are standard minimum if manufacturing for aircraft and aerospace applications. Since commercial sheet metal bending can be done with less concern for stresses caused during forming operation, the radius can be near zero for thin sheet metal.
Here you can specify many of the sheet metal specific properties including bend radius, K-factor, and bend relief dimensions. These can be fixed values or formulas based on the material thickness. (Note: you can find all of this information for your chosen material and thickness in our bending calculator as well.)A minimum radius of bend is specified for each type of aircraft sheet metal. The minimum bend radius is affected by the kind of material, thickness of the material, and temper condition of the material. . but it is a good practice to double check. For this layout example, use the minimum radius chart in Figure 2 to choose the correct bend . Table Of Contents. There are no headings in this document. . • Enter the precise sheet thickness and desired inner bend radius. • The calculator will instantly provide the K-factor, Y-factor, and neutral layer position, crucial for accurate bending calculations. . In sheet metal bending calculations, the impact of different material .
minimum sheet metal hamtramck radius
maximum thickness sheet metal bending
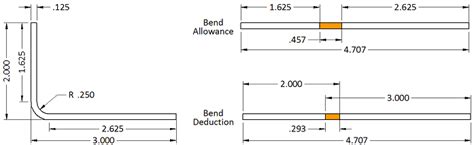
$144.99
sheet metal minimum bend radius chart|304 stainless steel bend radius