mig welding sheet metal upside down It cannotbe stressed enough! When MIG welding in an unfamiliar position, it is all about control. This is control over the situation, control over the precautions and safety, and finally, control of your welding capacity. Control gives you a better sense of your surroundings . See more For instance, the best way to conceal such a junction box is to use a large, deep 4-11/16" square metal box (which you need for the cubic inches), then stick a 2-gang "mud ring" on it, then stick plain 120V receptacles or switches there, fed by totally separate 120V / #12 wires.
0 · vertical mig welding tips
1 · vertical down mig welding
2 · overhead mig welding tips
3 · overhead mig welding techniques
4 · overhead mig welding settings
5 · mig welding overhead videos
6 · mig vertical up welding technique
7 · how to mig weld overhead
This Rhino Box is the most versatile box on the market. It has ten (10) potential openings. It can be used as a catch basin, distribution box, pump chamber, meter pit, and much more. The Polylok 24" Rhino Box makes even the toughest applications a breeze with its strength and versatility! Accepts 6" pipe with the use of Polylok 6" grommets!
Sparks are just a part of life when it comes to welding. Due to the nature of the heat source and the fact you are melting metal, it may seem like a no brainer: protect yourself. Always wear your helmet to keep your face and eyes safe. In normal circumstances, MIG welding can allow sparks to jump and . See more
The key to MIG welding upside down is keeping your feed regular and your arc short. While you are in a less than exciting position to be . See moreWhen creating a stable weld upside down, it’s essential to remember techniques designed to improve the weld’s stability. When welding, . See more
It cannotbe stressed enough! When MIG welding in an unfamiliar position, it is all about control. This is control over the situation, control over the precautions and safety, and finally, control of your welding capacity. Control gives you a better sense of your surroundings . See moreWleding upside down can take some major pratice. When welding inverted you must think safety first. Hot metal fragments and sparks can fall down on the fabricator, in this guide we cover how to weld in an upside down position.
Every welder offers a method for welding upside down. In this video, we see one of these methods#co2_upside #co2_upside_welding #upside_welding #weld_upside. I don't have any tips for welding upside down, aside from keeping bodyparts away from drips. Perhaps moving the torch faster, thus keeping the weld pool smaller will prevent it . If you are frequently welding, whether it be for work, for a hobby, or to repair a broken or damaged item for someone, there’s a good chance that sooner rather than later, you’re going to end up welding overhead or upside . You can MIG weld vertically by using a metal-transfer mode that freezes the puddle fast enough to keep it from dripping. The popular short-circuit mode can weld vertically both up and down, but has metal thickness limitations.
Mig welding sheet metal requires precision and control to prevent warping or burn-through. A thin wire and low heat settings are essential. Mig welding, also known as Gas Metal .
Still, it’s possible to weld thin sheet metal using the MIG (GMAW), TIG (GTAW), and stick (SMAW) processes. But MIG and TIG provide the best results. This article will teach you how to weld thin gauge metal using each arc . Can anybody provide any tips on MIG welding steel upside down. I'm repairing the sill on my MGB and whilst I can lay a reasonable weld down "the right way up" it all goes to . Find below the MIG Welding Sheet Metal Settings Chart which displays the recommended settings for welding different gauge thicknesses of sheet metal. To ensure .
The last thing you want is large blobs of molten metal burning through to your skin in the middle of a weld. 10 Tips and Tricks For Welding Upside Down! – Conclusion. Hopefully, with the tips and tricks we’ve .
5.i always start the weld on one piece of metal (the thickest), and then move over 1/8" to where I need to be. This helps alot on thin sheet which is mainly what I do. 6. If you can turn it upside down or on its side, do it! So much easier. I'm self taught, never even seen anyone else weld so I expect my technique is rather odd. Move faster or turn the wire down. A skilled weldor won't pile on so much extra metal so less warping will occur and there will be less grinding. Very, very few people are going to be able to O/A weld sheet metal without making . If I try bridging the holes with weld they only grow larger. This is really frustrating me, my welder is a very old Migatronic Autoweld 140 but I have recently had it checked over by a very experienced weldor who recknos that it is A1 so the problem must be my rubbish welding, the old metal or a combination of the two! I'm ok with welding generally, been using gas for years, and MIG for the last 3 or 4, I'm replacing the back wings and boot floor on the Jag, and came to need to do a bit of welding upside down, and couldn't get a neat weld at any price, to the point of .
Here’s a complete guide on how to weld thin metal with a MIG welder without warping. . Try welding a T-joint on thin sheet metal to practice heat control on . Weld two 300 mm x 300 mm sheets and measure any warping. How flat can you keep them? Upside-Down Practice: Try welding in the overhead position to improve puddle control. Start with . The Best Way to Weld Upside Down. Also known as an overhead weld, welding upside down can be a great challenge. This is especially true for a welder that has not used this technique before. The reason for the name of upside down, or overhead weld, is because the welder is actually above the head of the person welding. this will work better for upside down welding,also ensure you point your torch forward a good angle, not straight up, and prepare to move forward before you would normally move if you were on the flat. If you really are welding straight up above your head, spot welds are just as good, let metal cool
fiber optic cable distribution box
Melted aluminum and filler metal can trap hydrogen gas from the atmosphere during welding, which then forms bubbles in the cooled metal. This leads to porosity. Welding Upside Down. Welding upside down, or in an overhead position, can be especially tricky when you’re trying to weld aluminum. Hi just wondering what the best practice / best tools would be to take down a weld on automotive sheet metal to get a seemless finish. I have been using a 5 inch angle grinder with a 120g flap disc but I don’t feel 100% consistent and am paranoid about taking it down to far or unevenly. 5 inch is potentially too wide and taking metal off the surrounding areas unnecessarily? Hi all, welding of my mini is going fine, practice makes perfect as they say. However I have done both rear arches and have had to weld upside down. This produced lots of blow throughs, blobbing of weld and wire burning back . Hi All, I've bee practicing welding sheet metal building up to a car restoration project. I'm using a Clarke 151TE with 0.8mm wire and Argoshield. Metal is 1mm Zintec with the coating ground back prior to welding. This is today's efforts and I'd greatly appreciate comments and guidance.
This video shows you how to properly execute a fillet weld in the 3F vertical position with the weld progression going down using the Gas Metal Arc Welding (. Stick welding is not a delicate process but with a proper setup and rod size, you can weld sheet metal with the SMAW. Unlike MIG and TIG, stick welding doesn’t require a shielding gas. . After chipping away the slag or brushing the silica remains from MIG welds, you must grind down the weld line to improve its appearance. Don’t press down . I was wondering if anyone is proficient in welding sheet metal overhead with a MIG? I need to weld in a few patches and as luck would have it, I'll have to do it upside down. I'm pretty new with the MIG but have horizontal .
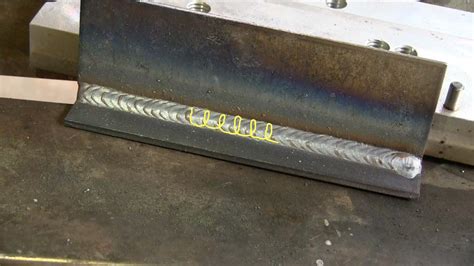
Hello everyone First post here. I'm looking for some advice on cutting mild steel sheet. Thickness between 0.8 and 4mm (plate) but predominately 2 to 3mm sheet. The plate and thin stuff is more on an ad hoc basis. Shapes will be varying sizes and dimensions with both straight edges and. For MIG welding sheet metal, it is often recommended to use an electrode wire of the smallest diameter to prevent burn-through and warping. The main reason to use a smaller diameter wire is that it takes less heat for melting and hence the metal around the weld is not heated . The floor pans are welded up from under the car with plug holes on floor pan, i.e. welding upside down against gravity. I have no problems welding on vertical or horizontal panels, but the inverted plug welds do not hold and appear to start to fall out of the plug hole. I have set my 170 mig with Argon/Co2 gas to a low wire speed and low wattage.
On the shed Saturday and welding an extra tool shelf on my pillar drill stand. Flat welding nice, no probs. Ditto on vertical. Underneath though - seemed like the wire was melting/burning back on same settings. Do I perhaps not have the wire feed roller torque down quite enough? TIA. G. I replaced some floor pans, inner and outer rockers, cab corners and some other sheet metal for a customer once... and that was the last time I ever did that. . Mig Welding Upside Down.. Originally Posted by zapster. Ahhh.. Back to the good'ol dayzzzzz..(drumroll please).. Zaps Harbor Freight 110 Mig!!!! Here it is semi done.. hi , yes , you work very close to right angles , as thin cutting discs dont like to be used on their flat , so you are basically holding the disc as if you want to chop through the weld spot , but you dont , and move side to side very very gently about half a mil or as the spot starts to flatten you can drop the angle to about 75 or 80 degrees . Here's some tips if you're having trouble mig welding thin sheet metal. Check out my custom mini parts available:Urchfab Front Subframe Kit: https://www.ebay.
3, Is your metal under the car as clean as the metal you are welding on the bench. My first choice would be to drop the voltage down a smidge especially as the panels won't have a heat sink, or increase the wire feed slightly and work faster, just be carefull in that increasing the wire speed will generally also increase the amperage so you may . I've used C-25 and Lincoln's L56 E70-S6 and it does spark some, but not "showers". I've welded in frame rails etc. but I was prepared for the sparks (leathers, position, etc.) Getting the metal relatively clean would help alot with both the sparks and the quality. Also, welding upside down and out of position takes practice to do decently... Find below the MIG Welding Sheet Metal Settings Chart which displays the recommended settings for welding different gauge thicknesses of sheet metal. To ensure optimal results, select the appropriate gauge thickness and refer to the corresponding joint gap, wire diameter, amperage, and voltage setting for your weld.
You can MIG weld vertically by using a metal-transfer mode that freezes the puddle fast enough to keep it from dripping. The popular short-circuit mode can weld vertically both up and down, but has metal thickness limitations. . This is why it’s best for thin sheet metal. For the same amperage, it can stabilize the puddle in the vertical . A good welder once told me the way to weld sheet metal with a MIG welder was to go downhill fast. The little 110 welders work OK, but it is a slow and tedious process. . Welding sheet metal upside down - johnny skeptical: 9/18/2022 07:02. RE: Welding sheet metal upside down - Brent1086: 9/17/2022 13:42;
vertical mig welding tips

Learn how to install 86mm electrical junction boxes for household outlets with ease and precision. In this video, we provide a step-by-step guide to wiring a.
mig welding sheet metal upside down|overhead mig welding tips