can you weld sheet metal with a flux core welder Conclusion . Whether you are experienced welder or just a novice, as a rule of . Favor boxes are great for parties. IBEX Packaging can help you get unique party or wedding favor boxes wholesale at cheap prices. Order to get free shipping.
0 · mig flux core welding basics
1 · flux core welding troubleshooting
2 · flux core welding techniques
3 · flux core welding setup
4 · flux core welding instructions
5 · flux core welding for dummies
6 · flux core welding for beginners
7 · flux core welding basics
Get custom jewelry boxes in bulk in a variety of material and color options. For example, you can order faux leather wholesale jewelry packaging boxes or burlap custom jewelry boxes. No .
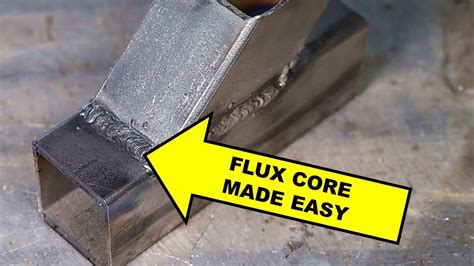
Welding body panels using flux-cored welding is possible, but not recommended. With FCAW the body panel will be more prone to burn through and warping due to the excessive, localized heat. There are some ways to increase your chances and make it happen.If you have a 220v machine and you do not have to weld very thin metal then I .There is a lot of confusion between the spot welding and tack welding.A lot of .
However, it has its own limitations and downsides. A few of these would be that .Conclusion . Whether you are experienced welder or just a novice, as a rule of . We’re going to explain the best ways to weld sheet metal with flux core so that even novice welders and DIYers can succeed on their first try. Once you settle on your welder, flux core welding thin sheet metal is pretty easy. Load the wire into the welder, feed it into the torch feeder, and lock it in. Feed the flux core wire through the torch. Cut the end and leave about .
Today we will be going over some tricks to weld thin gauge sheet metal like body panels while avoiding wrapage. I go over 2 different techniques and several .
mig flux core welding basics
Welding sheet metal with flux core can be daunting, even for experienced welders. This method, often used for constructing and repairing without shielding gas, requires precise technique and a steady hand. Flux core welding, also known as flux-cored arc welding (FCAW), is a welding method that utilizes a continuously fed electrode with a flux core. The flux core acts as a shielding agent, protecting the weld pool from contaminants . In this guide, we're diving deep into the art of flux core welding, breaking down the process step by step. Whether you're a greenhorn or a seasoned welder, this guide is your ticket to unlocking the secrets of . Welders can struggle with thin sheet metal because the hot arc warps or burns through the metal easily. Even professional welders flounder with welding thin stock at times. Still, it’s possible to weld thin sheet metal using the .
For general purpose mild steel welding applications, a flux-cored wire with the designation E71T-11 can be used in any position, is available in a wide range of sizes and provides excellent welding characteristics for both thin .
flux core welding troubleshooting
Welding body panels using flux-cored welding is possible, but not recommended. With FCAW the body panel will be more prone to burn through and warping due to the excessive, localized heat. There are some ways to increase your chances and make it happen. We’re going to explain the best ways to weld sheet metal with flux core so that even novice welders and DIYers can succeed on their first try.
Flux core welding is an advanced welding technique that uses a special shielding gas to join metallic materials. Unlike gas metal arc welding (GMAW), flux core requires a shielding gas and the ability to arc weld without the need for an electrode.
Once you settle on your welder, flux core welding thin sheet metal is pretty easy. Load the wire into the welder, feed it into the torch feeder, and lock it in. Feed the flux core wire through the torch. Cut the end and leave about 1/4 inch of wire stick out. Today we will be going over some tricks to weld thin gauge sheet metal like body panels while avoiding wrapage. I go over 2 different techniques and several .
Welding sheet metal with flux core can be daunting, even for experienced welders. This method, often used for constructing and repairing without shielding gas, requires precise technique and a steady hand. Flux core welding, also known as flux-cored arc welding (FCAW), is a welding method that utilizes a continuously fed electrode with a flux core. The flux core acts as a shielding agent, protecting the weld pool from contaminants and atmospheric gases. In this guide, we're diving deep into the art of flux core welding, breaking down the process step by step. Whether you're a greenhorn or a seasoned welder, this guide is your ticket to unlocking the secrets of mastering flux core welding, especially when dealing with delicate 22-gauge sheet metal.
lowes metal to wood fence brackets
Welders can struggle with thin sheet metal because the hot arc warps or burns through the metal easily. Even professional welders flounder with welding thin stock at times. Still, it’s possible to weld thin sheet metal using the MIG . For general purpose mild steel welding applications, a flux-cored wire with the designation E71T-11 can be used in any position, is available in a wide range of sizes and provides excellent welding characteristics for both thin and thicker material.
Welding body panels using flux-cored welding is possible, but not recommended. With FCAW the body panel will be more prone to burn through and warping due to the excessive, localized heat. There are some ways to increase your chances and make it happen. We’re going to explain the best ways to weld sheet metal with flux core so that even novice welders and DIYers can succeed on their first try. Flux core welding is an advanced welding technique that uses a special shielding gas to join metallic materials. Unlike gas metal arc welding (GMAW), flux core requires a shielding gas and the ability to arc weld without the need for an electrode.
Once you settle on your welder, flux core welding thin sheet metal is pretty easy. Load the wire into the welder, feed it into the torch feeder, and lock it in. Feed the flux core wire through the torch. Cut the end and leave about 1/4 inch of wire stick out. Today we will be going over some tricks to weld thin gauge sheet metal like body panels while avoiding wrapage. I go over 2 different techniques and several . Welding sheet metal with flux core can be daunting, even for experienced welders. This method, often used for constructing and repairing without shielding gas, requires precise technique and a steady hand. Flux core welding, also known as flux-cored arc welding (FCAW), is a welding method that utilizes a continuously fed electrode with a flux core. The flux core acts as a shielding agent, protecting the weld pool from contaminants and atmospheric gases.
lowes galvanized sheet metal roofing
In this guide, we're diving deep into the art of flux core welding, breaking down the process step by step. Whether you're a greenhorn or a seasoned welder, this guide is your ticket to unlocking the secrets of mastering flux core welding, especially when dealing with delicate 22-gauge sheet metal. Welders can struggle with thin sheet metal because the hot arc warps or burns through the metal easily. Even professional welders flounder with welding thin stock at times. Still, it’s possible to weld thin sheet metal using the MIG .

flux core welding techniques
Standard Die International is a full-service precision metal stamping & deep drawn parts company for a growing list of industries. Get a free quote today! (800) 838-5464
can you weld sheet metal with a flux core welder|flux core welding troubleshooting