boring operation in cnc machine Boring machining is a subtractive manufacturing process that uses a specially designed cutting tool to enlarge an already drilled or cast hole. Therefore, the primary function of boring is not to create new holes but to . Check out our guide to the best money making projects to produce with your CNC. Includes tips and tricks for making the most profit with your machine.
0 · used cnc horizontal boring machine
1 · small horizontal underground boring machines
2 · small cylinder boring machine
3 · large cnc horizontal boring mill
4 · horizontal boring and milling machine
5 · cnc horizontal boring machine
6 · cnc boring mills for sale
7 · boring head for cnc mill
Expert metal fabricators are needed to bend, weld, and manipulate metal parts, ensuring that the metal parts fit perfectly once assembled. Metal fabricators are essential to modern manufacturing because they bring metal's aesthetic appeal and practicality to life through various processes.
used cnc horizontal boring machine
large metal brackets heavy duty for overhead storage
In the CNC boring process, the continuous cutting is easy to cause tool wear and damage, which further results in reduced dimensional accuracy of hole boring and increases .By understanding the different types of boring tools, selecting the right tool for the job, and implementing proper machining techniques, machinists can achieve optimal results in their . Boring machining is a subtractive manufacturing process that uses a specially designed cutting tool to enlarge an already drilled or cast hole. Therefore, the primary function of boring is not to create new holes but to . How Does Boring Machining Work? The boring machining process typically unfolds on a lathe or CNC milling machine, both of which deploy a specialized boring tool known as a boring bar, fitted with an apt cutting insert. .
“The CNC boring is an extensively automated process that turns raw material into definitive designs with remarkable precision.” The CNC .
Boring operation is continuously inspected by measuring systems – dimensional stability and surface roughness are both monitored. In such case, modern CNC boring machines have an .In machining, boring is the process of enlarging a hole that has already been drilled (or cast) by means of a single-point cutting tool (or of a boring head containing several such tools), such . In CNC, we’re used to the idea of either drilling and reaming or interpolating a hole. So when does this boring method come into play? The answer is that you generally use one for larger holes when tolerances are . As CNC machining became more commonplace in the 1970s, mechanically operated boring machines gave way to computer-controlled models. The process is typically done on a lathe using a cylindrical tool with a cutting .
In CNC machining, boring technology is used as a precision machining process with a spindle mounted sleeve. Boring is a machining process in which the internal surface of a workpiece is cut by a rotating tool on a boring machine to .
In the CNC boring process, the continuous cutting is easy to cause tool wear and damage, which further results in reduced dimensional accuracy of hole boring and increases the surface roughness.By understanding the different types of boring tools, selecting the right tool for the job, and implementing proper machining techniques, machinists can achieve optimal results in their CNC boring operations. Boring machining is a subtractive manufacturing process that uses a specially designed cutting tool to enlarge an already drilled or cast hole. Therefore, the primary function of boring is not to create new holes but to process existing holes. This technique is utilized when an application requires greater accuracy and exceptional finish.
small horizontal underground boring machines
How Does Boring Machining Work? The boring machining process typically unfolds on a lathe or CNC milling machine, both of which deploy a specialized boring tool known as a boring bar, fitted with an apt cutting insert. Importantly, an initial hole birthed by drilling or casting methods is a prerequisite for the boring operation. “The CNC boring is an extensively automated process that turns raw material into definitive designs with remarkable precision.” The CNC boring offers accuracy and efficiency faster than any other process in the modern industrial manufacturing world.Boring operation is continuously inspected by measuring systems – dimensional stability and surface roughness are both monitored. In such case, modern CNC boring machines have an inbuilt adaptive control system that permits adjustments in the cutting parameters on automatic without any manual intervention.In machining, boring is the process of enlarging a hole that has already been drilled (or cast) by means of a single-point cutting tool (or of a boring head containing several such tools), such as in boring a gun barrel or an engine cylinder.
In CNC, we’re used to the idea of either drilling and reaming or interpolating a hole. So when does this boring method come into play? The answer is that you generally use one for larger holes when tolerances are tight. There’s a limit to how accurately we can make a hole using interpolation with an endmill.
As CNC machining became more commonplace in the 1970s, mechanically operated boring machines gave way to computer-controlled models. The process is typically done on a lathe using a cylindrical tool with a cutting insert called a boring bar. This is also why it’s sometimes incorrectly referred to as “internal turning.”In CNC machining, boring technology is used as a precision machining process with a spindle mounted sleeve. Boring is a machining process in which the internal surface of a workpiece is cut by a rotating tool on a boring machine to determine the precise hole diameter and surface quality.
In the CNC boring process, the continuous cutting is easy to cause tool wear and damage, which further results in reduced dimensional accuracy of hole boring and increases the surface roughness.By understanding the different types of boring tools, selecting the right tool for the job, and implementing proper machining techniques, machinists can achieve optimal results in their CNC boring operations. Boring machining is a subtractive manufacturing process that uses a specially designed cutting tool to enlarge an already drilled or cast hole. Therefore, the primary function of boring is not to create new holes but to process existing holes. This technique is utilized when an application requires greater accuracy and exceptional finish. How Does Boring Machining Work? The boring machining process typically unfolds on a lathe or CNC milling machine, both of which deploy a specialized boring tool known as a boring bar, fitted with an apt cutting insert. Importantly, an initial hole birthed by drilling or casting methods is a prerequisite for the boring operation.
“The CNC boring is an extensively automated process that turns raw material into definitive designs with remarkable precision.” The CNC boring offers accuracy and efficiency faster than any other process in the modern industrial manufacturing world.Boring operation is continuously inspected by measuring systems – dimensional stability and surface roughness are both monitored. In such case, modern CNC boring machines have an inbuilt adaptive control system that permits adjustments in the cutting parameters on automatic without any manual intervention.
In machining, boring is the process of enlarging a hole that has already been drilled (or cast) by means of a single-point cutting tool (or of a boring head containing several such tools), such as in boring a gun barrel or an engine cylinder. In CNC, we’re used to the idea of either drilling and reaming or interpolating a hole. So when does this boring method come into play? The answer is that you generally use one for larger holes when tolerances are tight. There’s a limit to how accurately we can make a hole using interpolation with an endmill. As CNC machining became more commonplace in the 1970s, mechanically operated boring machines gave way to computer-controlled models. The process is typically done on a lathe using a cylindrical tool with a cutting insert called a boring bar. This is also why it’s sometimes incorrectly referred to as “internal turning.”

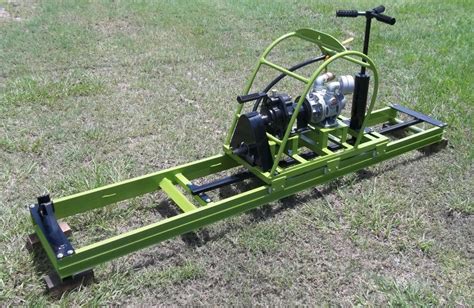
Depending on the pattern and type of sheet metal, you can use several different kinds of equipment to make a cut. You can use an electric saw for simple lines, or you can try tin snips, dremels, or metal nibblers for complex designs with curved lines.
boring operation in cnc machine|small cylinder boring machine