is flux core welder good for sheet metal Welding body panels using flux-cored welding is possible, but not recommended. With FCAW the body panel will be more prone to burn through and warping due to the excessive, localized heat. There are some ways to increase your . Junction boxes come in various sizes, and the screw size depends on the specific box size. For smaller junction boxes, #6 (3.5mm) screws with a length of 0.75 to 1 inch (19 to 25mm) are commonly used.
0 · mig flux core welding basics
1 · flux core welding troubleshooting
2 · flux core welding techniques
3 · flux core welding setup
4 · flux core welding instructions
5 · flux core welding for dummies
6 · flux core welding for beginners
7 · flux core welding basics
CAD/CAM software is a computer-aided design and manufacturing program for CNC machines, which helps users to do automatic CNC machining in industrial manufacturing. CAD makes designs more manageable and accessible, while CAM redefines how manufacturing works. CAM uses digital codes to quickly convert CAD-generated models into physical products.
Welding body panels using flux-cored welding is possible, but not recommended. With FCAW the body panel will be more prone to burn through and warping due to the excessive, localized heat. There are some ways to increase your .
Today we will be going over some tricks to weld thin gauge sheet metal like body panels while avoiding wrapage. I go over 2 different techniques and several . Flux-cored welding is ideal for welding outdoors. Learn some techniques when using this process for welding mild steel.
How to weld sheet metal with flux core. Prepare your workpiece. Set up the metal. Adjust the welder to the proper settings. Weld the sheet metals. Remove spatter and slag. To sum up everything. Choosing the appropriate . The Yeswelder 135 is the best flux core welder for beginners because it offers automatic (“Synergic”) adjustability making it easier to weld without any adjustments. It also .
9.995.009.995.99
9.999.995.00
Is Flux Core Welding Good For Sheet Metal? Flux core welding can be too aggressive for thin sheet metal, potentially leading to warping or burn-through. MIG or TIG welding is typically recommended for precise sheet metal . Flux core welding refers to utilizing a continuously-fed wire electrode that is filled with flux – flux, when burned during the welding process, creates an atmosphere around the welding process that protects the weld . Flux core welding offers advantages such as deep penetration and high deposition rates, making it a suitable method for welding thin sheet metal. It is important to be aware of the challenges, such as heat control and warping, . Flux Core Welding Sheet Metal uses gas-less flux core wire which means you don’t need gas. The wire contains “Flux” which will burn while you weld. . Usually the reference table inside your welder is a good place to start. .
For sheet metal ideally you’d want to go thin wire MIG, it’s much cleaner than flux core and you can get it in .025 wire. However I’ve used .035 flux core to do some body projects with no issues, it takes longer you won’t be able to run a full bead and has way more spatter you need to brush and grind down, but you can definitely do it. I have used gasless flux core to do 20 gauge floors up to 24 gauge quarter panels. All butt joints no lap. Single spot weld, move etc. till panel welded in. I have the the .024 wire and c25 also, it is higher quality, but when just doing spots the flux core was acceptable if set up properly. I did fight pin holes more with the flux core. You are simultaneously trying to conquer the toughest things for a beginner welder: thin material, round tubing, gas-less flux core (which is typically not used on <1/16"), and limited adjustability on the welder. Gas-less flux core is generally regarded as a "hot" process which is why it's not easy to run on thinner material.
pictures of metal awnings on houses
Dive into the world of flux core welding with the Arccaptain MIG200! Our comprehensive guide unveils the secrets, techniques for mastering this challenging yet rewarding skill. From adjusting machine settings to addressing common challenges. Discover the finesse of flux core welding with our step-by-step walkthrough.The actual difference between flux core and gas is really how clean the weld will be. Flux core "spits" more, because it is protecting the weld from oxygen and contaminates by boiling off inside of the weld and gassing out. That is why you get the little slag balls all around the weld. Hobart’s little flux core welding machine is one of our review’s best flux core welders. This is a well-built and capable brand-name welder that can weld up to 3/16 inch thick steel. For thicker materials, you will need a more powerful flux core welder, such as .Generally, mild steel is used as the base material when flux welding sheet metal, and the welding rod should be made of the same material. . What is a flux core welder good for? A flux core welder is a type of welding machine that is commonly used to repair, assemble and fabricate metal components. Compared to other welding processes, flux .
Successful flux-cored welding. Creating a successful flux-cored weld (or any arc weld for that matter) requires more than just memorizing the correct parameters and gun travel guidelines. Only through practice and learning to read the weld pool will you be able to consistently achieve sound flux-cored welds. The best welders for sheet metal is a MIG or TIG welder due to their precision and control. Key specifications include a wide amperage range for better . S7 TIG Welder stands out with its good heat control and reliability. With an amperage range of 10-200A, it delivers precise welds for sheet metal without causing warping or distortion .Hello I plan to tack weld some sheet metal with 0.030" flux core wire and I'm wondering to prevent burning through, what sort of backing should I.
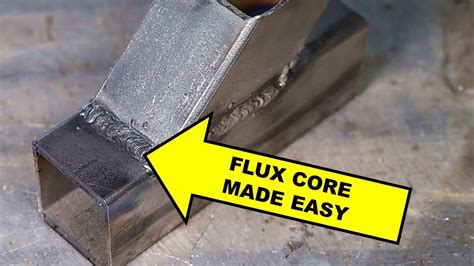
I've made videos in the past about welding 22 or 24 gauge steel with gas-less flux core wire, I thought I'd give it one more shot here after being a little m.A Chicago Electric Flux Core 125 Welder from Harbor Freight is used to weld an automotive patch panel into place fixing a lower fender rust hole. Special th. Learn about flux-core welding, including how to weld with a flux-core welder, common problems when welding with flux-core wire and tips on safety. . The space needs to be dry, clear of flammable materials and have good ventilation. Keep a fire extinguisher nearby. Caution. . While flux-core welding works with dirty or rusty metal better .
The Blue Demon E71TGS Flux Core Welding Wire is an ideal wire for sheet metal repairs and on any type of steel. It is a premium quality flux core wire designed for welding carbon steel. The unique quality of this product is that you do not have to use a .Keep up the good work! . a Flux Core welder is a terrible tool for the job. Reply reply [deleted] • very good to know. im planning to scratch straight lines and 90° angles in the paint around the rusted spots, and cut my sheet metal to fit as close as possible so that i only have a small seam that needs bondo. i figure that will hopefully . YESWELDER 135Amp MIG Welder,110V Flux Core Welder Flux MIG/Lift TIG/Stick 3-in-1 Large LED Digital Display Welding Machine IGBT Inverter Welder FLUX-135PRO - Amazon.com . FLUX-135PRO : Material .My little harbor freight flux core welder is just fine! It runs a good bead, and I’ve used it quite a lot for driveway repairs and teaching people. A stick welder will get the highest quality for the lowest price. . They used to use EXX24 and EXX28 rods on sheet metal before GMAW came around. Stick will serve you well as a hobbyist, I think .
This is especially important for weld strength when welding thick metal, which is what flux core welding is designed for. In addition, post-heating relieves the residual stress on the base metal, and you don't have to clean hard spatter. In addition, to successfully weld flux core, you will need a 10-15 degree travel angle.Flux core's wire is usually bigger than mig wire and it has a higher melting point so you need more amps and voltage in order to do a decent minimum weld. So the minimum parameters needed to do a decent weld are usually too hot for 16 gauge. Usually anything under 1/4 inch thick is mig welded and above that is SMAW/FCAW/MCAW. Can the Titanium Easy-Flux 125 Flux Core Welder be used for Auto Body Repair? Lap, butt and plug welds are demonstrated on 22 gauge (.030") auto body sheet .
Welding a bunch of different thickness material and shapes with the Titanium 125 flux core welder from Harbor Freight. Doing 16 GA. (Yes I know for you car g.Flux core LOL No MIG Yes. MIG welding stands for "Metal- Inert Gas." By definition MIG requires a bottle of inert shielding gas, often 25% CO2 and 75% Argon. This is ideal for things like auto body tnin sheet metal. Although a seperate shield gas is often used industrially for flux core welding. Some wire types don't need an external shield. Wondering if it's possible to butt weld automotive sheet metal with a flux core welder? This video can help answer that question by using a Harbor Freig.
I've done sheet metal repairs in some nasty stuff with flux. I run .045 wire on straight CO², 25.5v, 190-220 IPM, for things like this. You should check to see if you can get a good spot weld on some clean, well grounded scrap. If you can, then it's likely either you're poorly grounded, or the surfaces are contaminated.Today we are going through some more gasless welding tips and tricks using flux core wire and looking at 4 ways you can spot weld thin sheet metal. Each one .
mig flux core welding basics
Flux Core Welding Chart for E71T-GS + Flux Core + Tubular on MIG Welder ( 0.040 Wire Diameter) As with the above-listed wire sizes, you will have to use varying settings for flux core welding with 0.040″ wire. If the wire will be used with 9.5mm worth of material, you should choose a voltage of 22.5 while maintaining a speed of 300.

Choosing the right CNC machining material is crucial for ensuring the quality of your parts and meeting the demands of your production projects. To help you navigate the material selection process effectively, we have prepared a step-by-step guide.
is flux core welder good for sheet metal|flux core welding techniques