sheet metal bending terminology This Komaspec guide provides an overview of the main sheet metal bending processes, the advantages and disadvantages of each, basic design considerations with sheet metal bending and material selection information. $304.50
0 · types of sheet metal bending
1 · types of sheet metal benders
2 · sheet metal bending guidelines
3 · sheet metal bending dies
4 · sheet metal bending diagram
5 · sheet metal bending design guide
6 · maximum thickness sheet metal bending
7 · flange length in sheet metal
Best Exterior Paint Colors for a Green Roof From farmhouses to cabins to large estates, these exterior color combinations for a metal green roof work each and every time. .
The following glossary of terms are standardized definitions used throughout the bending industry. The definitions were developed by the Bender-Roller Committee of the American Institute of Steel Construction, of which Kottler Metal Products Inc. is an active member.Depending on the material shape our customers choose to use for their .
Despite the widespread use of curved structural steel members, detailed .
exterior bakelite electrical box
Defining basic terms in sheet metal bending. Reader questions about V-groove bending, bend allowances, and k-factors. By Steve Benson. July 9, 2024. FIGURE 2. This CNC system has multiple cutters that cut V-grooves .This Komaspec guide provides an overview of the main sheet metal bending processes, the advantages and disadvantages of each, basic design considerations with sheet metal bending and material selection information.Shane. September 14th, 2024. Bending/Folding. Table Of Contents. Sheet metal bending is a fundamental forming process that alters the geometry of a metal sheet or panel by creating angular changes along a linear axis. In a series of posts we are going to review the most important sheet metal design terminology — Bend Allowance, Bend Deduction and K-Factor. With over 35 years of experience, the TriMech Group offers a comprehensive range .
My extensive experience has allowed me to become an expert in the fields of sheet metal fabrication, machining, mechanical engineering, and machine tools for metals. I am constantly thinking, reading, and writing about .
types of sheet metal bending
Tooling Terminology; Design Guidelines; Gauge Chart; 3 Types Of Bending. There are three types of bends used to form metal that any sheet metal engineer or press brake operator must be familiar with; Air Bending, Bottom Bending and Coining. Air Bending. Air Bending is the most common type of bending process used in sheet metal shops today.This guide explores sheet metal bending processes, materials suitable for bending, factors to consider and design tips for bending sheet metal parts. . Thick materials can also be bent as well as thin materials. Note that the term ‘sheet metal’ is typically used to refer to materials that are under 3mm in thickness. Sheet metal bending .

To help you navigate this field, we’ve put together a guide to five common sheet metal fabrication terms, explained in detail. Tooling: Hard, Soft, and Hybrid Tooling and Die Sets. Sheet metal fabrication often involves custom-made die sets that are used to cut, shape, and form metal. Tooling is the process of designing and engineering the .Urethane and Polyurethane are interchangeable terms for an artificially created rubber. . Special punches are not required for this method of fabrication. The sheet metal is placed flat on top of the urethane pad before the punch tip s forced down into the pad. . By forming the sheet metal into this feature 180° bends can be formed in a .
Bend Radius - As a rule, inside bend radius should be equal to material thickness. When the radius is less than recommended, this can cause material flow problems in soft material and fracturing in hard material. Bend Relief - When a bend is made close to an edge the material may tear unless bend relief is given. Figure "A" shows a torn part.
FAB402's metal fabrication term glossary. Learn more about the metal working industry and the terms you might hear in a metal shop like ours! Skip to content. Call Today: 402-413-2183. . Sheet Metal: Thin, flat metal pieces used in fabrication projects. Sheet metal can be cut, bent, and formed into various shapes and sizes. . Comprehensive glossary of metal fabricating term and related resources. Our Sites . FMA; The Fabricator; FABTECH; Canadian Metalworking; . Taking automated tube bending to the next level. 3. 3 areas of safety manufacturing shops should focus on. 4. EMJD acquires Proto Sheet Metal Products. 5. What I learned on my trip to EuroBLECH. Industry .
Adjustable models allow for extremely versatile bending of both sharp and large radius pieces further improving their versatility. Imagine being able to do a single stroke U bend with the same tool you bend 90° bends with. For a shop on a limited budget a few sets of Rolla-V dies can set you up to bend a very wide variety of geometries. Media
Bottom bending is the process of stamps the radius of the punch tip into the work piece. This differs from Coining, which puts the entire surface of the work piece under such tonnage that it begins to flow. when Bottom Bending the die angle should match the intended angle of the work piece, adjusting a few degrees for Spring Back, hence the existence of 88 ° punch tooling to . Know Your Ductwork Fitting Terminology. Posted on October 29, 2019; by admin; . E.P. Homiek Sheet Metal Fabrication & HVAC Supply, with two convenient locations in Lakewood, NJ and Union, NJ, provides one- to two-day turnaround on all residential and light commercial ductwork, as well as one- to two-hour emergency fabrication service, rapid .Tooling Terminology; Design Guidelines; Gauge Chart; Box Bending. Box bending can be rather tricky with sheet metal because of the geometry of a press brake. typically the upper beam or punch holder will get in the way of very deep boxes. When bending with large returns there are a few tricks outside of just tooling selection. When bending a 2 .
Curling sheet metal is the process of adding a hollow, circular roll to the edge of the sheet. The curled edge provides strength to the edge and makes it safe for handling. Curling is different than a tear drop hem because in a curl the edge finishes inside itself, where a . Sheet metal bending is the process of using a CNC or manual brake to bend or form sheet metal into 3-dimensional shapes. What sounds like a relatively simple process actually involves a significant amount of complicated .
exterior junction box cover
Study with Quizlet and memorize flashcards containing terms like Stamping, Water Jet Cutting (Waterjet), Gauge and more. . Round duct manufacturing and sheet metal fabrication machine. Plasma Cutting. A process that cuts through electrically conductive materials by means of an accelerated jet of hot plasma. Typical materials cut with a plasma .Tooling Terminology; Design Guidelines; Gauge Chart; Air Bending. Air bending is the most common type of 3 Types Of Bending used in sheet metal shops today. In this process the workpiece comes in contact with the outside edges of the .Bend relief – A special bend tool is used to facilitate easier bending of sheet metal, mitigating the risk of unwanted cracks or tears. Bending – A metal forming process wherein a die is used to facilitate angular displacement of a metal stock material. Blank – The sheet metal used to make a product. Also, the piece resulting from the . Sheet metal fabrication is a simple yet diverse manufacturing operation. For product designers, companies and entrepreneurs that are new to interfacing with sheet metal companies, there are a number of terms denoting key operations you should know. From design to production and assembly, these terminologies will remain pervasive in your discussions, and having a full .
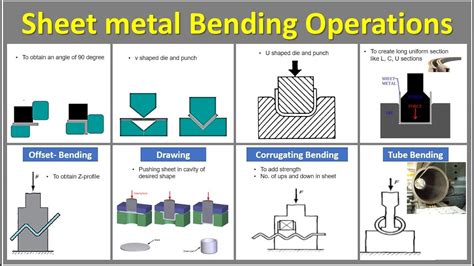
Press brake is a common device used in sheet metal fabrication. It can bend the metal sheet into the required shape through pressing down the die. . Advanced Terminology and Techniques. Bend allowance. Bend allowance refers to material deformation or elongation required by forming a specific bending angle. It is calculated according to . In the simplest terms, on our CNC sheet metal brakes, the bottom die needs sufficient contact at two points on the part, so that the bend is successful and the part doesn’t slip off the die. . Navigating the world of sheet metal bending might seem daunting at first, especially when transitioning from 2D designs to 3D parts. However .
types of sheet metal benders
sheet metal bending guidelines
Metal Fabrication Terminology 101: A Beginner’s Guide. Metal fabrication processes are a combination of various techniques that produce products from raw materials and semi-finished metal products. The output of metal fabrication may be used to complete a whole project or be the desired final result in itself. Basic Metal Fabrication JargonWiping die bending, also known as edge bending, is performed by holding the sheet between a pad and die then sliding the wiping flange across the face pushing and bending the sheet metal which protrudes from the pad and die. The flange is driven by an upper shoe and the die is supported by a lower shoe. Besides bottoming, coining, and air bending on a press brake, sheet metal shops also use stamping. Stamping is when flat sheet metal is fed into a stamping press as a blank or from a coil. The stamping press uses a punch and die to form the metal into a predetermined shape. Using Good TermsSheet metal bending terms. Learn with flashcards, games, and more — for free.
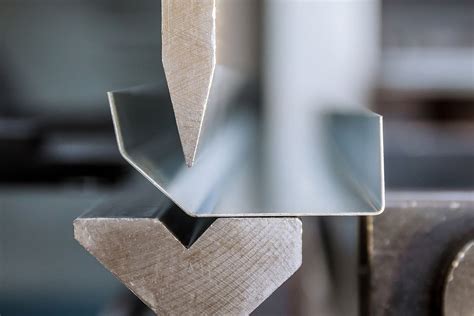
exterior electrical box shallow
Sheet Metal Fabrication Resources. . Fabrication Formulas Expand Fabrication Formulas submenu Collapse Fabrication Formulas submenu. Bend Angles; Bend Allowance; Bend Deduction; Inside Setback; Outside Setback; K-Factor; Y-Factor; Tooling Terminology; Design Guidelines; Gauge Chart; Arc Length. Leave a Reply. Your email address will not be . Die Casting and Sheet Metal Bending: Cost-Benefit Evaluation. Die casting and sheet metal bending represent two distinct manufacturing processes, each offering unique advantages and trade-offs in terms of cost, complexity, and scalability. Die casting, characterized by its high tooling costs and production setup, excels in producing complex .
sheet metal bending dies
They are the end of through rods that are used to hold in the sides of old masonry buildings. One can often see them in old European buildings. 37 votes, 11 comments. 2.6M .
sheet metal bending terminology|sheet metal bending design guide