process of making sheet metal The process involves the sheet metal being placed over a die, then pressed with a punch into an open cavity, causing the material to undergo plastic deformation. The process allows for precisely made complex shapes . Sheet metal fabrication is a process of working with metal, used in various industries, ranging from construction and automotive to warehouse and electronics. It involves transforming flat sheets of metal into functional components and structures through cutting, .
0 · types of sheet metal fabrication
1 · sheet metal operations with diagrams
2 · sheet metal manufacturing process types
3 · sheet metal fabrication capabilities
4 · perforating operation in sheet metal
5 · how to fabricate sheet metal
6 · disadvantages of sheet metal
7 · basics of sheet metal fabrication
From intricate engine parts to sturdy steel bridges, metal fabricators contribute to various industries and projects important to societal development. Understanding what the role entails can help you decide if it's the right career path to pursue for you.
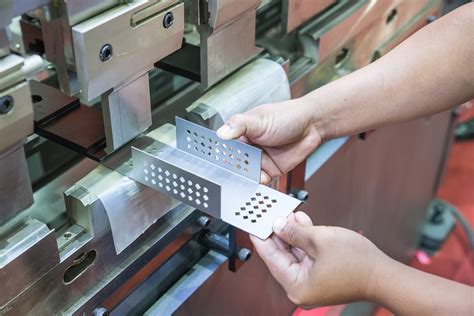
The sheet metal fabrication process is an intricate journey from raw metal to a finished product. It involves various steps, ensuring the final product meets specific standards and functions. In this article, we’ll explore the nine vital steps in sheet metal fabrication, providing valuable insights .
The process involves the sheet metal being placed over a die, then pressed with a punch into an open cavity, causing the material to undergo plastic deformation. The process allows for precisely made complex shapes .Sheet metal fabrication is a versatile approach that begins with the selection of a flat metal sheet, typically steel, aluminum, or stainless steel, and transforms it into the desired component through various processes.
The manufacturing & design guide. Learn how to effectively design sheet metal parts. This guide starts with the basics and moves toward design best practices and advice on material .
The art and science of sheet metal fabrication involve a series of meticulous processes, from designing and cutting to bending and welding. This article unpacks the top ten technological processes, guiding you through each . Sheet metal stamping is a high-precision manufacturing process in which sheet metals are transformed into various shapes and parts. It involves the use of dies and stamping presses to achieve specific shapes, making it ideal for producing components for the automotive, aerospace, electronics, and other industrial sectors. There are four basic stages in the process of making sheet metal: melting, pouring, pickling and lastly, rolling and annealing. Sheet metal is made for a wide range of purposes, from automotive parts to rain gutters to medical equipment and building components. The type of metal used is specific to the intended application, but the process of .sheet metal funnel making,sheet metal funnel layout,.. sheet metal funnel pattern,.. how to make a sheet metal funnel,.. sheet metal funnel . funnels, ducts etc. are made from a flat sheet of metal. The process being known as tin .
5. Sheet Metal Processing The raw material for sheet metal manufacturing processes is the output of the rolling process. Typically, sheets of metal are sold as flat, rectangular sheets of standard size. If the sheets are thin and very long, they may be in the form of rolls. Therefore the first step in any sheet metal process is to cut the correct shape and . Pressing rivets is an essential process in sheet metal fabrication, and it requires a great deal of skill and experience to master. . When done correctly, polishing can make a sheet metal object look new. Sheet Metal Fabrication Tools. One of the most critical aspects of sheet metal fabrication is the tools used. Various tools can be used .
Bending is a fundamental sheet metal forming process that transforms 2D flat parts into 3D components with precise angles and contours. This operation is primarily executed using a press brake in conjunction with specialized bending dies. The process involves applying controlled force to deform the metal along a linear axis, creating permanent .
types of sheet metal fabrication
sheet metal operations with diagrams
aluminium enclosures for electronics india
Welding sheet metal is a very critical process within the modern concept of manufacturing. The construction of metal structures, pipelines, and tanks is among the most common applications for sheet metal welding. Though the process is rather straightforward, it can be complex to achieve quality and efficiently weld thin sheet metals. Understanding the key . For the shearing process in sheet metal, sheets are fabricated into multiple components – all of which can now be used to manufacture different items. The metal material itself is cut precisely and accurately, with the objective being the overall removal of any unwanted or unrequired particles. Accuracy is the name of the game here, and the . Comparison Table: Different Die-Making Methods for the Sheet Metal Drawing Process As previously mentioned, sheet metal drawing dies can be manufactured through a variety of methods. These methods include traditional machining, grinding, and advanced techniques such as Electrical Discharge Machining (EDM) and Computer Numerical Control .
One of the most common sheet metal processes is bending, in which a machine called a brake is used to bend sheet metal to an angle up to 120°. This is perhaps the most important process when making sheet metal brackets, since virtually all brackets incorporate at least one bend. Other sheet metal processes must also be used. Sheet metal cones are versatile and indispensable in a wide range of applications, from ductwork in HVAC systems to chimney caps and funnels. Whether you need to replace a damaged cone or create a custom design for your project, learning how to make a sheet metal cone can save you time and money. In this step-by-step guide, we will walk you through the . The Advantages Of Precision Sheet Metal Fabrication Process. The precision sheet metal fabrication process is ideal for high-quality manufacturing due to the various benefits it offers. For example: Customization: This process allows manufacturers to produce parts and components tailored to meet precise requirements. They just need to modify .
To ensure the accuracy of your sheet metal blanking process, make sure to choose the right blanking method, design the punch and die properly, maintain the blanking equipment, and implement regular inspections and quality control measure. 0 Comments. Submit a .It is a distinct process of making a hole in sheet metals. It is characterized by: (a) The punch is sharp and pointed tool which is able to penetrate or pierce through the sheet metal. (b) There is no scrap from the hole. (c) The hole has rough flanges around the hole. Notching: Notching is removing small quantity of material from the edges of .
Various sheet metal materials are suitable for notching, such as aluminum, copper, stainless steel, and more. Notching is also a common process when you create a sheet metal prototype. The Process of Making Dimples in .
They cover how to make SHEET METAL DOG TAGS and SHEET METAL VISE JAW COVERS. Step 1: Video Walkthrough . To do this step I will be using a bar folder but the process can be done with a sheet metal brake as well. Your goal .Sheet metal is one of the very convenient ways that is used in metal working and it can be mended and cut into various shapes and dimensions. A wide range of products are manufactured with the use of sheet metal making it an essential . Less common sheet metal deformation processes include wheeling, which is used to make compound curves in sheet metal, and rolling, in which sheet metal is fed between a pair of rollers to reduce its thickness (and/or increase consistency in thickness).. Some processes sit halfway between cutting and deformation. For example, the process of sheet metal expanding .
One significant advantage of the embossing process in sheet metal working is the improvement in structural rigidity. The added texture can provide increased strength and resistance to bending or denting, making the final product more robust and durable. Improved Heat Dissipation; After finalizing on all the details, the engineering team will make the final sheet metal enclosure drawing. Here, thorough calculations are done to establish the stress levels on the various parts of the enclosure. This evaluation and calculation will dictate the subsequent process of sheet metal enclosure. Step 2: CuttingBecause metal can be formed into thin sheets, the metal needs to be processable. To do this, metals are melted into a processable, uniform ingot to be later pressed and flattened into a sheet. Regardless of the type of metal used, the metal stage always comes first in the sheet metal-making process. 2. The Pouring Stage. Once the metal is .Metal stamping or metal pressing is a process that consists of a series of processes actually, including bending, punching, and blanking with tools and dies, coining, flanging, etc. The process gives the metal sheet the desired shape according to your design. It is one of the most used metal forming processes.
Sheet metal fabrication is an essential process for many industries, enabling the creation of complex and precise metal components. Understanding the various fabrication techniques is crucial for effective decision-making, cost optimization, and quality control.
Ah, I've thought about doing that before but each step of the coin making process was a roadblock for me. Making a thin enough sheet, having a press, being able to make the steel stamp to get the impression onto the coin, etc. . If you ultimately want to make coins I would forget trying to make sheet metal and focus on making coins. Using the .Sheet metal is a metal that is shaped into thin, flat pieces by hot and cold rolling industrial process. Sheet metal is one of the basic forms of metalworking and can be cut and bent into various shapes. How is sheet metal made? Sheet metal is made by running hot slabs of metal through a series of roughing rolling stands that makes them thinner .
Key Considerations for Bending Sheet Metal: Material Thickness: The capability to bend metal cleanly is dependent on its thickness.Thicker metals require more force and potentially specialized equipment. Bend Radius: The inside radius of the bend should be compatible with the material properties to avoid cracking or breaking.Each type of metal has a minimum bend . Making a sheet metal bracket involves a series of steps: selecting the appropriate metal, accurately measuring and marking your design, cutting the metal, bending it into the desired shape, and finally, finishing and installing it. . Fabrication is at the core of custom sheet metal brackets. The process consists of several crucial steps to .
alro metals sarasota fabrication
sheet metal manufacturing process types
If you currently have stainless steel appliances in your kitchen, you might want to add in a bit of brass and/or black to create an interesting mix. To keep your kitchen looking cohesive, don’t mix too many finishes, colors, and styles in the same room. The Cabinet Gallery Utah – .
process of making sheet metal|basics of sheet metal fabrication