how to decrease a gap when welding sheet metal patch #1. Hi. I recently butt welded in a patch patch and after cleaning up the weld noticed a small section where it didn't fully penetrate and after planishing the welds I can see . Cajons aren’t just made from box-jointed plywood anymore, but now include fiberglass and acrylic in addition to a modern wooden stave-constructed version. Gon Bops Rumbero cajon Most major brands have dozens of cajons to satisfy nearly any niche.
0 · wrong way to butt sheet metal
1 · sheet metal in place welding
2 · how to butt weld sheet metal
3 · blow through welding sheet metal
$249.99
Today we're going to demonstrate how to butt weld sheet metal using a Lincoln Electric mig welder. Like anything, there's a right way and a wrong way to butt weld patch panels on a car.. Intergrip panel-alignment clamps work like miniature butt-weld clamps that align panels edge-to-edge and surface-to-surface, leaving an ideal 0.040″ gap for full weld .
#1. Hi. I recently butt welded in a patch patch and after cleaning up the weld noticed a small section where it didn't fully penetrate and after planishing the welds I can see . Make sure your weld gap is as small as possible, less than 1/8” ideally. A non-ferrous backing bar or spot weld pliers can provide material support and absorb more heat to minimize burning through. Be careful to only grind the welds and to keep your grinder away from the patch or the original metal. It's very easy to thin out the sheet metal and weaken the patch, especially . Leave a gap: When MIG welding a patch panel on your car body panels you should think of leaving small gaps between the patch panel and the original metal. During the welding process the metal will get hot and the gap a .
Assuming your mig welding, Cooling the weld faster with an air nozzle will reduce the warpage. It prevents the heat ring from expanding further out. For patch panels toss the .
Still, it’s possible to weld thin sheet metal using the MIG (GMAW), TIG (GTAW), and stick (SMAW) processes. But MIG and TIG provide the best results. This article will teach you how to weld thin gauge metal using each arc .
We’ll use TIG welding for the rear patch. The first steps are identical to the front — overlapping, adjusting and clamping the patch panel into place, scribing the edge, and then trimming and adjusting the panel to get a . In practicality, I wouldn't gap automotive gauge sheet metal. If I could fuse it without filler, I would. Less chance of popping a hole in it, and less work to finish it afterwards. For the non experienced a zero gap butt weld is not easy and even impossible at times. Just a 1/16 lap weld on a flange will be hard enough to get done nicely. REMEMBER you are NOT WELDING A BEAD on the panels. This will be 1/2 a million stitch welds for you. Weld a spot and move to the other side of the panel a spot is 1 tack BTW.
Where possible try and get the two pieces of sheet to be as level with one another as possible. Reason, if you have say 1/3 of the thickness standing higher than the other then once you have welded it when it cones to . There are 2 basic methods to MIG welding large gaps, the first is to use filler metal to help cover the gap that is cut to size to fill the gap and help make the weld a smoother process. The second is to do a root pass to fill the .
#weldingtrick #stickwelding #6010Today I pass on a trick my Millwright friend Bruce gave to me. If your in a bind and need to weld a uneven or wide gap this .
Use this amazon link to buy ANYTHING and it will throw some pennies in the jar toward Mike Fn Garage thanks for watchinghttps://amzn.to/2JPFrYh No gap works best, Penetration with sheet metal is no problem. It's how you weld that is important. If gaps works for you then fine. We've had no problems butting then together. I can actually have better welds butted together then most professional bodyman can weld with a gap. It's all in the technique. What ever works for you is important.
You'll never warp another panel again after watching this video. This is a realtime, step by step demonstration that shows how to mig weld sheet metal withou. My site for purchasing T-Shirts www.acdesignsgarage.comMy PO Box Adress, PO Box 782 Troutman NC 28166In this video I share with you two different ways.
The Pneumatic Perfect Panel Prep Tool allows you to create a 45° valley in between two panels to help get strong & smooth weld seams! Get Pneumatic PPPT Here.When working with sheet metal, how do I reduce the width of a gap in a miter corner? Share Add a Comment. Sort by: Best . Design it so that you have a uniform gap across the seam then the fabricator can fill it in with a weld and grind smooth. . You said "working with sheet metal" it in itself, is an analog medium. And is difficult to .
wrong way to butt sheet metal
On this episode of Make It Kustom I show you how to butt weld thin sheet metal body panels using tig welding. This is a fender repair on a customers Fox body. Check your gap after every 2-3 hits regardless as you can make the gap too tight and it may overlap or cause a high spot in the panel. Here we can see the gap all tightened up and ready to weld. This tight gap across the weld seam allowed me to mostly fusion weld the seam and keep the heat and warpage down. Welding sheet metal with a flux core is feasible for thin materials. . Whether tackling a repair job or working on a custom creation, mastering flux core welding on sheet metal opens the door to a realm of metalworking possibilities. . such as a 0.030″ diameter, which suits sheet metal applications better due to its lower heat input .Here's some tips if you're having trouble mig welding thin sheet metal. Check out my custom mini parts available:Urchfab Front Subframe Kit: https://www.ebay.
Hey SCHOONER,If it were me,I would but weld it.The main thing with getting a good finished product is panel fitment.Take alot of time makeing the panel fit perfect,the maximum gap iI would allow for is 1/16 of an inch.After the panel fit to my likeing,I would tack weld it on the corners,and one in the center.Here comes the hard part...TAKE YOUR TIME!!!!DO NOT GET . The edge of the patch acts as a guide so you get a nice straight cut and the airsaw blade is thinner then a conventional cut off wheel so you get a nice tight gap for butt welding. The quick and dirty method that I normally use . Today's auto sheet metal is a different critter than the old 30's and 40's cars I used to mess with (and messed up a few). Its thinner and 'high strength', which sure seems a lot more like working with a Potato Chip instead of leather. Was my first attempt at MIG on sheet metal and it came out like a pro did it! Actually, I didn't use the gap clamps, just used deep reach vice-grips and eyeballed a gap for a butt weld. Keys to a good job are get the metal very clean, the gap accurate to about 1/32" then just spot weld. NEVER run a bead that generates a visible blue zone bigger .
Sometimes you might want to or need to butt weld sheet metal patch panels for rust repairs. This video shows two ways to do butt weld sheet metal for qualit. In this video I show how to Mig weld any gap. This process is useful when you get your cuts off a little bit or your angles are off a little. This happens to. Butt welding is the type of weld where the edges of the sheet metal meet up with no overlap. This type of weld is very useful for body word repairs as once the weld is finished it can be ground down flush with the metal work leaving an invisible repair. The main issue with thin body work is the fine line between correct penetration and blowing .

husky red metal tool box
On thicker material, you don’t need to worry about this much, as it doesn’t react as easily. Sheet metal is a different story entirely. Sheet metal is typically used for panels where being straight is important. Rocker panels, floor pans, patch panels, the straighter the better. Point being, the key to straight panels is heat mitigation. On this episode of make a custom I pull the 81 G10 Van in for a rust repair patch step-by-step mig welding.Check out how to make your own tucking fork here:h. Hot Rods Mig weld pin holes in sheet metal hack. Discussion in 'The Hokey . Some pin holes no doubt were because I didnt get two welds to touch enough.Some because I didnt have a perfect gap around the patch section.In the end zero is what im shooting for.Got my patching done with out distorting the lower skin on the door which makes it a lot .
After reading several posts here about how butt welding patch panels is better than lap welding I decided to try it on my latest project. . If this was your first ever sheet metal butt weld I'd try more practice first. . Sounds like you had too big of a gap or the heat too high. When I butt weld all you can see on the inside is the weld .MIG is one of the best ways to weld 20-gauge sheet metal. MIG welding is one of the simplest to use for welding. . For the inert gas, aim at having more argon to carbon dioxide – 75% argon to 25% carbon dioxide. Argon helps reduce cases of spatter as it carries less heat. If you are going to be welding 304 stainless steel the such for wires . 11. Sheet Metal Tips. As mentioned in the introduction, sheet metal work is a different animal than steel beams. Any of the above practices can be useful in mitigating distortion in sheet metal, but there are additional practices that can come into play and perhaps save the day. These include: Water-Cooled Jig
husky metal tool box for truck
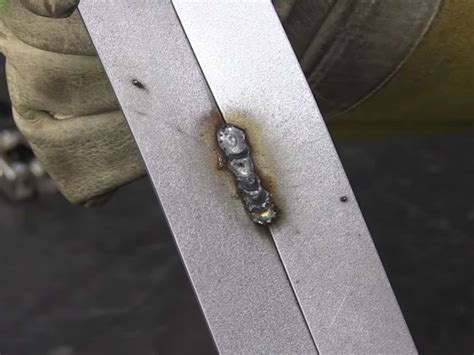
Learn how to get started woodworking and set up shop for less than $1000. Download my FREE GUIDE https://theweekendwoodworker.com/tww-.
how to decrease a gap when welding sheet metal patch|blow through welding sheet metal