concept sheet metal Our 31-page digital guide provides information and guidance on all of the basic concepts of sheet metal design, including metal selection, bending, fasteners, finishes and more. We’ll send the Sheet Metal Design 101 Guide to the email .
Midwest Turned offers CNC precision machined components and services. Get high-quality products from a trusted precision machining company. Contact us.
0 · working with sheet metal basics
1 · types of sheet metal fabrication
2 · sheet metal layout techniques
3 · sheet metal design standards
4 · sheet metal design guidelines pdf
5 · sheet metal design and fabrication
6 · basics of sheet metal fabrication
7 · basics of sheet metal design
Precision Machining: Our state-of-the-art CNC (Computer Numerical Control) machines are equipped with high-precision tools and multi-axis capabilities, enabling us to achieve tight tolerances and intricate geometries required for telescope parts. We meticulously follow design specifications and dimensional requirements to ensure the accurate .
The sheet metal design process involves conceptualizing, drawing, and creating detailed plans for cutting, shaping, and joining metal. It’s all about turning metal sheets into durable, functional, and aesthetic products for various industries, .
These basic sheet metal fabrication guidelines include important design considerations to help improve part manufacturability, enhance cosmetic appearance, and reduce overall production time. Sheet Metal Fabrication is . In this article, we will provide a comprehensive guide to sheet metal fabrication design, including tips for material selection, geometric constraints, and cost-effective design strategies.
Sheet metal fabrication is a highly versatile process used in the manufacturing industry to create various parts and components. This process involves cutting, forming, and assembling metal into different shapes and .Sheet metal fabrication is the process of forming parts from a metal sheet by punching, cutting, stamping, and bending. 3D CAD files are converted into machine code, which controls a .
Our 31-page digital guide provides information and guidance on all of the basic concepts of sheet metal design, including metal selection, bending, fasteners, finishes and more. We’ll send the Sheet Metal Design 101 Guide to the email . Sheet metal is a metal such as aluminum, brass, titanium, nickel, tin, and copper processed into thin flat pieces like foils, leaves, and plates. Since they are formed to be light, thin, stable, and elastic, they are extensively used .Sheet metal prototyping, a fundamental phase in product development, involves transforming designs into tangible models using techniques like cutting, bending, and joining. This process . Sheet metal fabrication, in brief, is the process of machining metal sheets to form metal parts or structural components of desired shapes and sizes.
The sheet metal design process involves conceptualizing, drawing, and creating detailed plans for cutting, shaping, and joining metal. It’s all about turning metal sheets into durable, functional, and aesthetic products for various industries, from aerospace to automotive.
These basic sheet metal fabrication guidelines include important design considerations to help improve part manufacturability, enhance cosmetic appearance, and reduce overall production time. Sheet Metal Fabrication is the process of forming parts from a metal sheet by punching, cutting, stamping, and bending. Fabricating objects and structures out of flat metal sheets is what we mean when we talk about sheet metal fabrication. Creating various components and pieces from multiple sheet metals is often the end goal of the processes used to treat sheet metal. In this article, we will provide a comprehensive guide to sheet metal fabrication design, including tips for material selection, geometric constraints, and cost-effective design strategies.
Sheet metal fabrication is a highly versatile process used in the manufacturing industry to create various parts and components. This process involves cutting, forming, and assembling metal into different shapes and structures. The first step in creating a sheet metal part is sheet metal design.
Sheet metal fabrication is the process of forming parts from a metal sheet by punching, cutting, stamping, and bending. 3D CAD files are converted into machine code, which controls a machine to precisely cut a flat pattern, which can be formed .Our 31-page digital guide provides information and guidance on all of the basic concepts of sheet metal design, including metal selection, bending, fasteners, finishes and more. We’ll send the Sheet Metal Design 101 Guide to the email you provide below. Sheet metal is a metal such as aluminum, brass, titanium, nickel, tin, and copper processed into thin flat pieces like foils, leaves, and plates. Since they are formed to be light, thin, stable, and elastic, they are extensively used in industries for cladding and covering purposes.Sheet metal prototyping, a fundamental phase in product development, involves transforming designs into tangible models using techniques like cutting, bending, and joining. This process demands precision, as even minor errors can significantly impact the final product.
Sheet metal fabrication, in brief, is the process of machining metal sheets to form metal parts or structural components of desired shapes and sizes.The sheet metal design process involves conceptualizing, drawing, and creating detailed plans for cutting, shaping, and joining metal. It’s all about turning metal sheets into durable, functional, and aesthetic products for various industries, from aerospace to automotive.These basic sheet metal fabrication guidelines include important design considerations to help improve part manufacturability, enhance cosmetic appearance, and reduce overall production time. Sheet Metal Fabrication is the process of forming parts from a metal sheet by punching, cutting, stamping, and bending.
electrical back box spacers
Fabricating objects and structures out of flat metal sheets is what we mean when we talk about sheet metal fabrication. Creating various components and pieces from multiple sheet metals is often the end goal of the processes used to treat sheet metal. In this article, we will provide a comprehensive guide to sheet metal fabrication design, including tips for material selection, geometric constraints, and cost-effective design strategies. Sheet metal fabrication is a highly versatile process used in the manufacturing industry to create various parts and components. This process involves cutting, forming, and assembling metal into different shapes and structures. The first step in creating a sheet metal part is sheet metal design.Sheet metal fabrication is the process of forming parts from a metal sheet by punching, cutting, stamping, and bending. 3D CAD files are converted into machine code, which controls a machine to precisely cut a flat pattern, which can be formed .
Our 31-page digital guide provides information and guidance on all of the basic concepts of sheet metal design, including metal selection, bending, fasteners, finishes and more. We’ll send the Sheet Metal Design 101 Guide to the email you provide below. Sheet metal is a metal such as aluminum, brass, titanium, nickel, tin, and copper processed into thin flat pieces like foils, leaves, and plates. Since they are formed to be light, thin, stable, and elastic, they are extensively used in industries for cladding and covering purposes.Sheet metal prototyping, a fundamental phase in product development, involves transforming designs into tangible models using techniques like cutting, bending, and joining. This process demands precision, as even minor errors can significantly impact the final product.
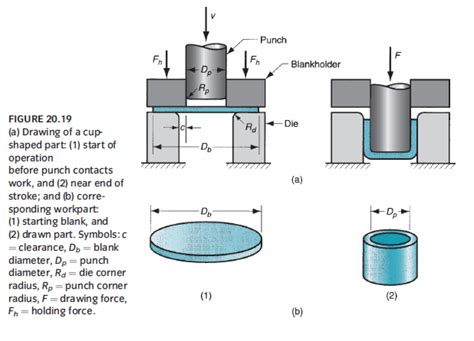
working with sheet metal basics
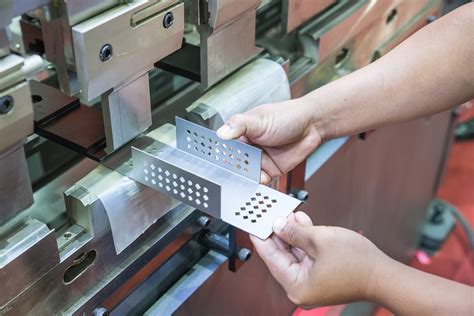
CNCPros.com offers a wide variety of parts designed to fit your Fadal like Ballscrews, ATC clips, spindles, resolvers, amplifiers, inverters and more – all on-the-shelf, ready-to-ship today! Lowest prices on the things you really need.
concept sheet metal|sheet metal design standards