flux weld thin sheet metal For general purpose mild steel welding applications, a flux-cored wire with the designation E71T-11 can be used in any position, is available in a wide range of sizes and . Make sure that your light fixture is big enough to cover the hole you need to make to install the electrical box. If you go to an electrical supply store, you'll find all kinds of electrical boxes. Some of them are specifically designed for remodeling work -- and are easier to attach than electrical boxes designed for new construction.
0 · mig flux core welding basics
1 · flux core wire welding techniques
2 · flux core wire welding instructions
3 · flux core welding videos youtube
4 · flux core welding techniques
5 · flux core welding for dummies
6 · flux core welding for beginners
7 · flux core welding basics
Selecting the appropriate electrical box depends on several factors, including construction, wiring method, devices, location, and safety. See more
Today we will be going over some tricks to weld thin gauge sheet metal like body panels while avoiding wrapage. I go over 2 different techniques and several tips so make sure you watch. Still, it’s possible to weld thin sheet metal using the MIG (GMAW), TIG (GTAW), and stick (SMAW) processes. But MIG and TIG provide the best results. This article will teach you how to weld thin gauge metal using each arc .
For general purpose mild steel welding applications, a flux-cored wire with the designation E71T-11 can be used in any position, is available in a wide range of sizes and . In this guide, we're diving deep into the art of flux core welding, breaking down the process step by step. Whether you're a greenhorn or a seasoned welder, this guide is your ticket to unlocking the secrets of . How to weld sheet metal with flux core. Prepare your workpiece. Set up the metal. Adjust the welder to the proper settings. Weld the sheet metals. Remove spatter and slag. To sum up everything. Choosing the appropriate .
The thickness of the metal is important, but 0.030” and 0.035” diameter wire overlap in what gauges of steel they’ll weld. If you don’t have a powerful machine or can only use 120-volt power, 0.030” wire is the best . One advantage of flux core welding for thin sheet metal is its deep penetration capabilities. The flux core electrode provides good penetration, resulting in strong and durable welds. Flux core welding is known for its high .
This article covers everything you need to know about welding thin sheet metal: from tips for beginners to advanced welding techniques that experienced professionals use under difficult circumstances.
Welding sheet metal with a flux core is feasible for thin materials. This process utilizes a flux-cored wire to shield the weld pool. Welding sheet metal, skinny gauge, is a valued skill with numerous applications in . When welding thin sheet metal with flux core, using the right techniques is crucial for achieving clean and strong welds. Here are some techniques to consider: Controlled heat input. Thin sheet metal is sensitive to .
mig flux core welding basics
sheet metal classes
While the specific material may not be critical, the form of the filler metal is important when working with thin sheet metal. 3. Adjust the Torch Angle . Double Pulse Mig, Flux-cored wire welding and MMA. Memory function. . This video was a tough one. I tried to find the easiest way to weld thin sheet metal with flux core. Flux core is usually used for heavier metals and is not .
Once you settle on your welder, flux core welding thin sheet metal is pretty easy. Load the wire into the welder, feed it into the torch feeder, and lock it in. Feed the flux core wire through the torch. Cut the end and leave about 1/4 inch of wire stick out. Sheet metal is metal that is processed into thin and flat sheets Trusted Source Sheet metal - Wikipedia In most of the world, sheet metal thickness is consistently specified in millimeters. en.wikipedia.org , which is where it gets its name. For sheet metal welding, you need to have much more skill and precision as compared to other forms of . How to Weld Thick to Thin Metal with Gasless Flux Core Wire - Trying out some TIps and Tricks for welding thick to thin metal with gasless flux core wire usi.
The Hobart Handler 140 MIG Welder is my top choice because of its versatility and user friendly interface. It is capable of welding thin sheet metals because of its low minimum amperage range and has a smooth and stable arc. It is ideal for hobby welders that can complete their sheet metal welding job without requiring a high duty cycle. The E6013 welding rod is the best to stick weld thin mild steel and is known as a sheet metal rod. An E6013 has a flux covering with high amounts of rutile. Rutile creates the smoothest arc with light penetration that won’t burn through the joint as easily as other rods.
sheet metal chassis processing technology
Welding thin sheet metal with flux core requires careful control to prevent burn-through. Use a low amperage setting and maintain a steady hand. Welding thin sheet metal can be tricky due to its susceptibility to warping and burn-through. Flux core welding offers a convenient solution, especially for outdoor conditions and windy environments. I am trying to still get some feedback about the best wire for my machine to use with thinner sheet metal. . from my experience you will not find a way to WELD with flux core on this thin material ( exhaust tubing ) even on the lowest setting - the lowest i have seen for mig on any of the 110 or 220 volt machines is Harbor Freight, maybe . Today we're flux core welding sheet metal. Last time we did a thin gauge flux core welding video we used 1/8" and got completely hammered for it not being th.#welddotcomLets weld some thin material with flux core!Join Weld.com today, get member’s perks and support the community! https://www.youtube.com/channel/UCM.
This video is a tutorial on welding thin metal with the UNIMIG VIPER 185Email: [email protected] of the thin gauge sheet metal are made from steel, stainless steel, aluminum or galvanized. It is imperative you consider the shielding gas, welding process, and electrode before welding 20-gauge sheet metals. . Lastly, do not try to use flux cored wires for thin metal sheets as they pass more heat to the base metal. Flux-cored arc .
Today we are going through some more gasless welding tips and tricks using flux core wire and looking at 4 ways you can spot weld thin sheet metal. Each one . Welding thin sheet metal is a challenge for any welder, but it can be even more daunting as an entry-level amateur or as a seasoned professional. For novices. . When welding thin metal with flux core or mig welding, you . Select Your Ideal Method of Welding Thin Metal. Welding reedy metal shouldn’t frighten you. It’s just one more part of the task that you should learn to master and develop your expertise. Not every one of us begins .
In this follow up to an earlier video, David covers ideal machine settings, weld positions, and contact tip to work distance using Lincoln NR-211 self-shield. In this video I demonstrate how to set up your mig welder so you can weld thin sheet metal. We also showed in this video how to make your pattern, fit and we. Shielded metal arc welding, also known as SMAW or stick welding, is a popular method for welding thin metal. This method uses an electrical current to create an electric arc between the base metal and a consumable electrode covered in flux. For thin sheet metal welding it can be 30 ampere while for thicker (e.g. 1/8” square groove weld)- it can go up to 220 ampere for example. GMAW-S gives low heat and makes it easy to use in all positions on sheet metal, low carbon steel, low alloy steel, and stainless steel sheet metal from 25 gauge (0.02 inch or 0.5 mm) to 12 gauge (0.1 inches or 2.6 mm).
We’ve been using this welder for a lot of years, for the price this welder is very convenient because you don’t have tanks of gas and it plugs into a regular.
Single spot weld, move etc. till panel welded in. I have the the .024 wire and c25 also, it is higher quality, but when just doing spots the flux core was acceptable if set up properly. I did fight pin holes more with the flux core. Even small stitches it was no contest for the C25 though. In my opinion flux core limited to spots only on thin .
In this video I show how to set up your mig welder to be able to weld on super thin metal with out warping it. I go through step by step comparing how to pre.
By understanding the unique challenges posed by welding sheet metal, you can tailor your approach to deliver exceptional results. In the realm of sheet metal welding, precision and attention to detail are paramount. Achieving clean and strong welds on thin metals requires meticulous planning and execution. Flux core welding (FCAW) is much easier to learn and master than stick (SMAW) or TIG welding (GTAW), but it can present many challenges for beginner welders. . 0.030” wire will weld 20 gauge to 14 gauge sheet metal, and 0.035” wire will weld 18 gauge to 3/16” thick steel. The thickness of the metal is important, but 0.030” and 0.035 .
Hopefully, somone with experience in sheet metal welding will come along. . Like ChevyTruckGuy said, flux core + thin panels = frustration ain: The best way Ive found to do it is to turn up the amperage and the wire speed above whatd be considered normal and hold the tip with one hand and hit the trigger with the other, and, stitch-weld it as .
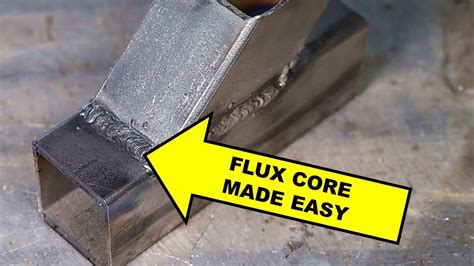
flux core wire welding techniques
sheet metal cnc laser cut exporters
Lastly, the recommended tap drill size is provided for each standard tap size. This .
flux weld thin sheet metal|flux core welding for beginners